Sand Bedding for dairy cows
Hard bedding has a negative effect on the time that cow to lies down and gets up to go to the feeder and drinker. It is also a stressor for cows and may cause mechanically joint pad inflammation. Since clean bedding means : “less mastitis, less milk loss, less flies, less foot disease, less somatic cells and less total bacteria” . It is very important for dairy farmers to do a comparison on the cost of using sand / straw / rubber mats becomes important for cows and farmers before making informed decision.
Sand
From a bacteriological point of view, sand is the first choice for the reduction of IMI caused by environmental bacteria.

As an inorganic material, it does not support the growth of environmental bacteria and it usually has lower bacterial counts than organic materials, so teat exposure is lower, as is the risk of mastitis in dairy cows. However, we must consider availability and price.
Also, it needs special manure handling systems which tend to be expensive. When new facilities are planned, arrangements can be made for the use of sand, but to use sand on a farm which is not prepared for this can be a huge problem.
It is also possible to recycle the sand to reduce bedding costs. Some farmers leave used sand in a pile for a few months and organic matter from manure is composted and reduced. Others, in larger units, prefer to wash the sand. In both cases, the goal is to obtain sand with less than 2% of organic matter.
Some types of fine sand become harder when in the freestall because of the weight of the cow. In this case, it is important to till it once a day or every two days, to achieve a correct protective effect against mastitis in dairy cows.
This is also important in order to avoid small piles of sand between freestalls. With this operation we have a better use of the sand and the comfort of the freestall is improved.
The following are cow litter materials and costs for stall beddings:
Sand as inorganic bedding material
As a cow bedding sand is preferred because of its soft and non-microbial inorganic structure. Sand considered the “gold standard” for US farmers. Various scientific studies have been carried out to ensure that the material in the bedding ( sand ) is inorganic sand animal litter. Each bedding material has advantages and disadvantages.
Table 3 Bacterial growth examined source Godden et al 2008
Bedding materials 0-72h | K. Pneumoniae (cfu /ml) | E. faecium (cfu/ml) | pH | C (%) | N (%) |
---|---|---|---|---|---|
Clean sand | 1.07a | -1.65a | 8.15A | 0.28A | 0.01A |
Recycled sand | 1.91b | 0.27b | 8.37B | 1.13B | 0.04A |
Digested solids | 3.16c | 0.09b | 8.90C | 46.22C | 1.99B |
Savings | 1.44a | -4.50c | 4.27D | 53.02D | 0.35C |
a-;Different superscripts indicate a significant difference (p<0.05) in bacterial growth amid bedding types at an incubation period of 72h.
A-CDifferent superscripts indicate a significant difference (p<0.05) in biochemical characteristics amid bedding types.
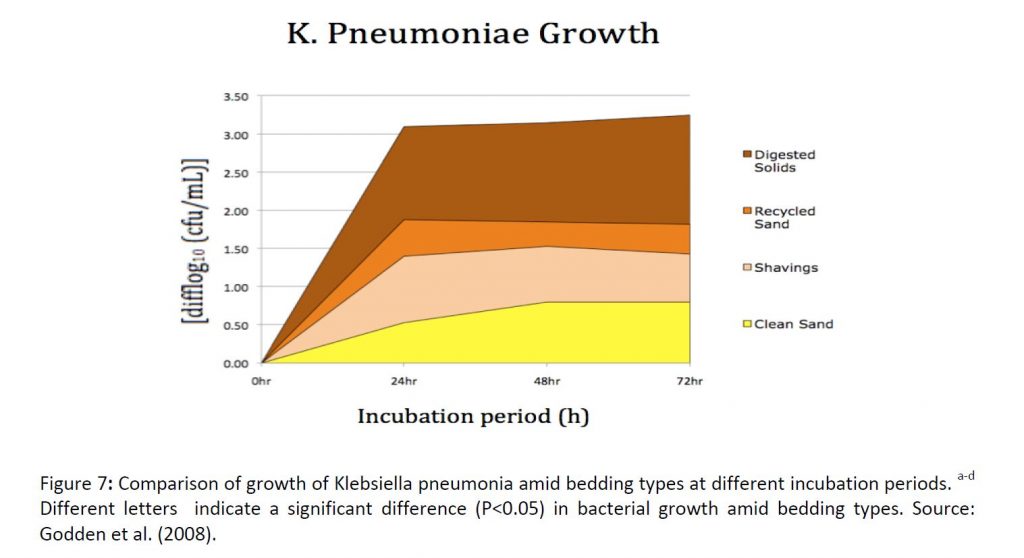
Sand has a positive influence on the production of dairy cows because
It provides a comfortable lying surface, which enhances overall cow health because of the following findings:
- Lover risk of bacterial infection: The inorganic characteristic of sand reduces risk of mastitis caused by bacteria in the bedding material, and therefore production losses are less compared to other bedding materials.
- Increased lying time:
- Increases rumination and blood flow to udder, which enhances milk production.
- Decreases stress hormone release, which improves overall health and well‐being of the cow, and increases production.
- Reduces stress on feet, and thus reduces the risk of lameness and the prevalence of claw lesions.
- Soft and cushioned (sand, straw or deep‐bedded sawdust) bedding increases recovery from lameness and other health problems, and therefore production.
Advantages of using sand bedding
- Sand as cow litter materials it takes the shape of the cow’s body and its physical structure. In hot conditions
- Lower bacterial levels and less mastitis due to environmental organisms such as E-coli and streptococci.
- Since it is an In-Organic material, the growth of bacteria is low. However, it should be taken into account that it has an important role in the spread of infections with its effect on hygiene in milking parlors.

- The loose sand on the walkways creates a better and more gripping with the added friction. Cow slippage can reduce in hot conditions. Provides better slip resistance.
- Less claw trimming is necessary because it provides homogeneous claw wear.
- Sand is a good material for quick drainage.
- Cows in the sand are clean, especially the udder area looks very clean and healthy. Clean animals Dirt score 1-2
Disadvantages of using sand bedding
- It creates problems at low temperatures due to its poor insulation properties.
- Sand (more or less) always contains a certain amount of moisture.
- In cold conditions, sand freezes, hardens, and becomes “sharp like a knife.” Cows prefer not to lie down in these cold and wet conditions.
- Loss of energy and (decreased lying periods) cause a decrease in milk yield.
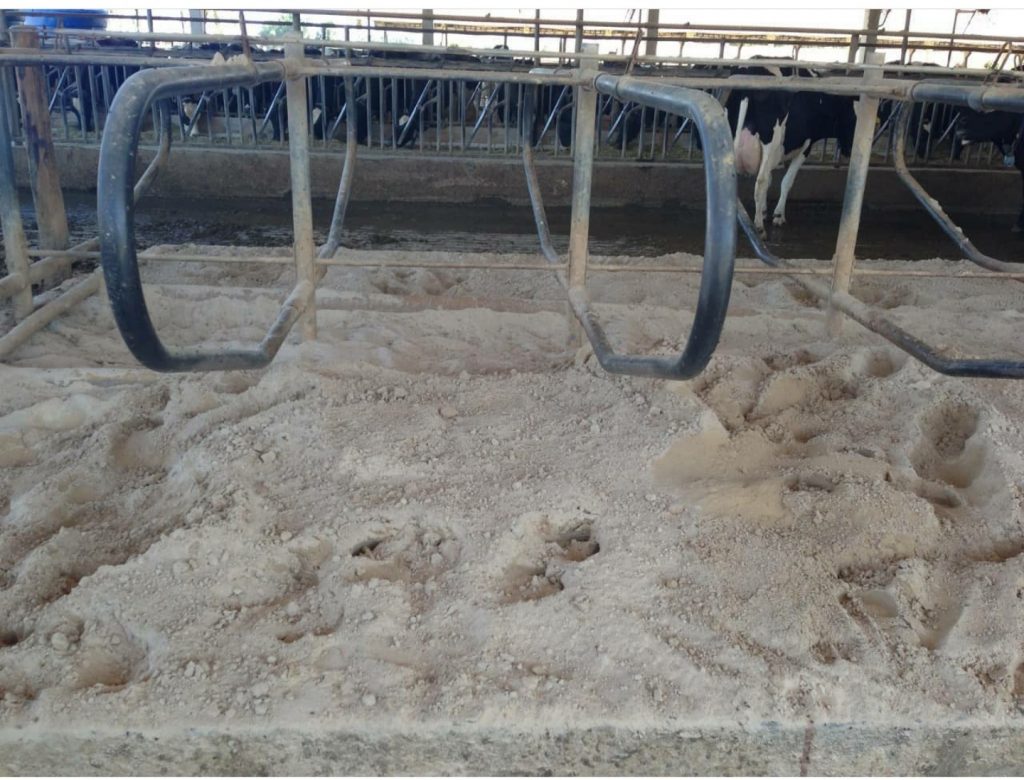
- The bedding sand should be leveled daily with a rake to ensure and maintain the comfortability of the cows.
- The sand must have a maximum granule size of 2 mm.
- The sand should not contain small, large or sharp stones. Especially small and sharp stones can get into their nails and sting.
- Sand can stick to the cow’s udder and it may not be easy to get rid of.
- It is important to clear all paths inside and outside of the barn, otherwise sand dunes will form
- Low-quality sand contains stones, which settle between the nails and injure the legs of animals.
- The stones in the sand get under the rubber mats and lift them. With the next wash, more dirt and sand gets under it, which increases the problem.
- Slip and fall increases due to the remaining sand on the walkways.
- Combination with slatted floors is not possible.
Sand use and management
- Sand is a material that MUST BE MANAGED VERY WELL and is a major factor in cost.
- Cows scratching the sand is one of the leading causes of sand loss.
- Old tires are placed in bed pits in the US to reduce daily sand loss (but not a convincing solution).
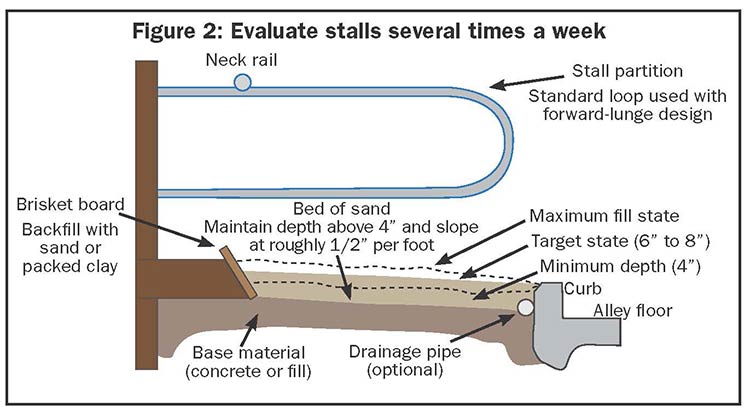
The deep stall pit should completely fill with sand . Sand height should be at least 45-60 cm.
- Excess moisture sludges and cools the sand bedding.
- Too dry sand will fly as dust. Eye irritation and Pnomeniya increase.
- Every day sand should be leveled and corrected between milking times at least 2-3 times. Otherwise, the bedding area will be hollow.
Every 1 cm of less sand = 11 minutes less lying time..

In order to compensate for the reduced sand at stalls, +1.5 cm, 25 kg of sand per animal per day should be added to the bedding. This means extra work, labor, vehicle expenses and materials.
KUM ve malzemeli derin durak ölçüleri
Cost of sand using
If we assume that this used sand material is recovered from 80% recycling! The reserve, which will meet the need for an additional 2 tons of sand and 25 tons of water (8+17= 25-€) per animal annually, must be obtained on site or within 3 km.
Calculations show: Per animal per year with 9 tons of sand approximately 3-€. The cost of sand management found to be 4- €/ animal. 110 tons of water per animal per year for washing sand and cleaning with water used; operating cost: 0,68 €/ton
The daily sand operating cost is calculated as 0.09-€/cow.
Sand-laden manure management systems : https://www.agproud.com/articles/55968-maximizing-roi-of-sand-laden-manure-management-systems

Applications and references
One of the exemplary leading farm which is a sand animal litter user in Turkey, is is ACIPAYAM ATASANCAK tarım işletmesi agricultural enterprise. In the farm where 950 cows are milked; 9,000 tons of water and 600 tons of sand are used daily. While 85% of the water and 80% of the sand used provide an economic contribution with the recycling system, it does not have a negative impact on the environment. 2014
ATASANCAK TARIM İŞETMESİ DATAS
Investments costs of sand bedding
Advantages
- In terms of economy, the initial investment cost of sand bedding is relatively low.
- Construction cost of deep bedding stall is 60-80 € cheaper than elevated stalls .
- Since the need for 9 square meters of 30 m3 concrete for the foundation construction of the elevated stall is eliminated.
- For the first filling, 1/2 m3 (average 500 kg) of bedding sand per animal is sufficient. (first sand 6.2-€/tone)
- With operating costs of 8 to 10 €/tones of sand
- compared to organic bedding $40 to $50 per tone lower.
Constrains
- Sand distribution vehicle (20 tons) cost 20-25.000€/unit
- Sand separation settling pond need ( manure / water / Sand)
- A sieve, regeneration and recycling system is required.
- Scrapers and manure pits will require expensive technology vehicles.
- A special filter system is required for reuse of sand, separating manure.
- If there is plenty of water in the flushing system, the sand will be moistened and cleaned.
- The structural feature of the sand is very abrasive, the concrete layer needs to be thicker in the cleaning methods with the flushing system.
- Annual concrete floor wear cost should be considered (depreciation)
- Barn equipment, pumps, Scraper systems, etc. will soon wear out due to high wear!!
- Sand will also cause the parlor equipment to wear out, and break down more frequently.
SAND Process

The floor sub mat POLSTA is used to reduce daily liter sand, straw, sawdust need and increase softness.
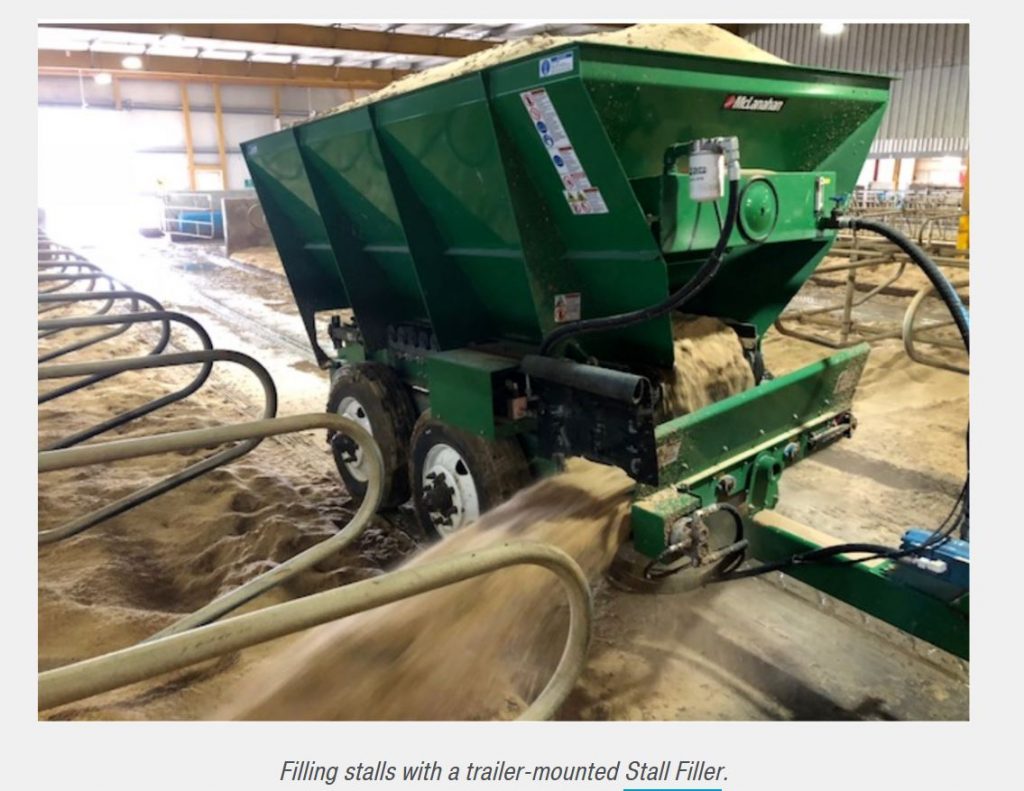
Calculations show: Per animal/ year with 9 tons of sand approximately 3-€. The cost of sand management found to be 4- €/ animal. 110 tons of water per animal per year for washing sand and cleaning with water used; operating cost: 0,68 €/ton. LİNK

The farms use sand generally do not use scrapers. sand has a very high abrasive effect on scrapers, all machinery, equipment and concrete. If a scraper is to be used, it must be special and rubber lipped. For this reason, it is generally cleaned by flushing system.

Vacuum cleans the alley in one pass, allowing more time to properly fill and groom freestall bedding. Minimized time in they alleyway means reduced wear and tear on equipment. In efficiency tests, Manure Vacuum was able to clean a 330 cow group (on 3x milking) in less than 10 minutes – including unloading! the Manure Vacuum replaces the need for pumps, augers, and concrete channels to transport manure from the barn to the storage lagoon or process facility.
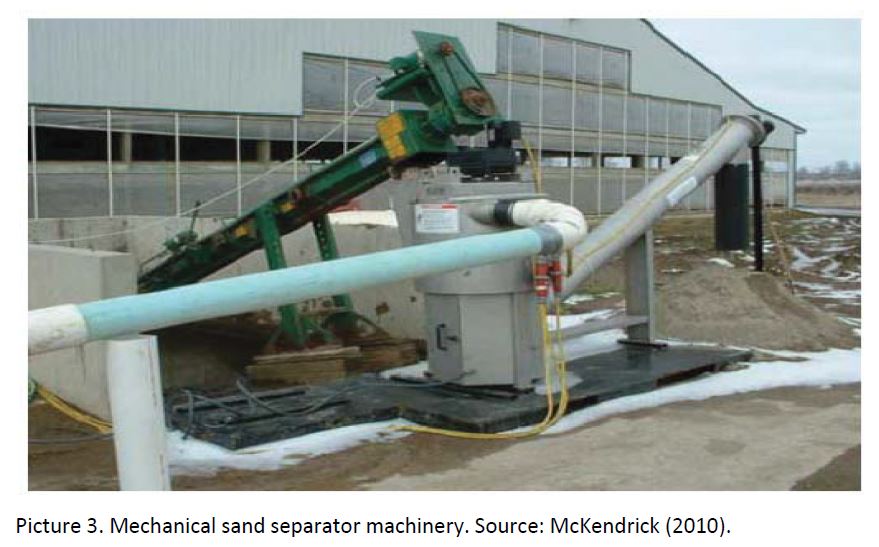
- Expensive technology manure disposal system is required.
- Expensive technology vehicles will be required for manure lagoons.
- Sand leveling tool and apparatus tractors
- Sand dispersing and distribution vehicles truck and apparatus
- High cost cleaning system
- Vacuum cleaning
- vehicles are expensive equipment
- Fuel, spare parts, maintenance nd high running cost
- Flushing system cleaning.
- The required infrastructure investment is very high and requires high maintenance cost.
- High volume water use and resources need.
- Large volumes of water capacity water tanks and engines are needed.
- Vacuum cleaning
- Special strainer system is required for reuse and recycling of sand, separating manure and sand.
- Sedimentation ponds and lagoons are required for separation as the manure mixes with the sand.
- The structural feature of the sand is very abrasive;
- C30 concrete wear an average of 4 cm of in 10 years. so the concrete layers need to be thicker
- Barn equipment, systems, pump, etc. will soon wear out due to high wear!
- Equipment wearing parts will need to be replaced.
- Sand will also cause wear on the milking equipment.
- Bio-gas and energy production is not possible unless sand is separated from the manure.
- Sawdust and similar substances should not be used.
- Combination with slatted floors is not possible
Referances https://www.mclanahan.com/blog/doing-these-3-things-will-allow-you-to-maximize-your-sand-bedding
From an economic point of view, sand is not economically positive as a bedding material
- Cows throw an average of 20 to 25 kg of sand out of bedding per day from each stall
- in order to compensate for the reduced sand at the stalls. require additional. 10-25 kg for each cow per day
- This means more work, labor and materials.
- In order to reduce daily SAND loss, put old tires or rubber mats but not a reliable solution.
- “USED OLD TIRE” is defined as HAZARDOUS WASTE according to Waste regulation
- Bio-gas and energy production is not possible unless sand is separated from the manure.
- A detailed and specific manure system is required.
- Extra wear and tear resistant equipment can cost more than the savings described above.
- Many manufacturers claim that the straw material is inexpensive, free and readily available.
- With $40 per tone, the price will be quite variable depending on seasonal and economic conditions, although straw is free, its actual price and storage costs can be quite high.
Chapter | Advantages | Constrains |
---|---|---|
Sand | -Comfort -inorganic -Dry -Cool -Traction | -Heavy -Freezes in cold weather -Labour intensive |
Cost | -Cheap if readily available -Financial cost can be recouped by well managed investment | -More expensive in areas further from beaches and rivers -Cost dependent of lorry transport |
Housing | -Soft bedding -Sand on concrete increases grip -Reusable if recycled | -Manure handling -Wearing of machinery -Recycling is expensive |
Behavior | -Laying times > 12 hours -Standing times < 2 hours -Sand provides cushioning and traction for rising and laying down -Increased walking behavior Increased feeding and drinking -Less stress | -Each 1 cm less sand= -11 minutes less laying time -Cows digging = loss of sand |
Health | -Significantly less environmental mastitis Lover bacteria counts in bedding -50% less coliform bacteria compared to saw dust in teat swabs -85% less Klebsiella compared to saw dust in teat swabs -42% less lameness -75% less hock abrasions | -Sand can be abrasive if the layer is too thin -More lesions on dorsal tuber calcis |
Production | -Increased laying times -Increased rumination + increased blood flow -Less stress = More production -Lame cows recover faster ( less production loss) | Takes time for cows get used to sand Slightly production loss possible during transition possible |
Legislation | -Solid floor is low NH3 emission system -Improved housing is a part of regulation to improve dairy cow welfare | Legislation due to change about spreading waste on fields |
Ethics | Sand approved by both utilitarian and deontological views for providing cow good comfort and improved health | Potential for sand to be marketed as a good animal welfare and mislead public as to poor management practices |
Bedding materials and liters comparison: Sand/ straw / Rubber mat
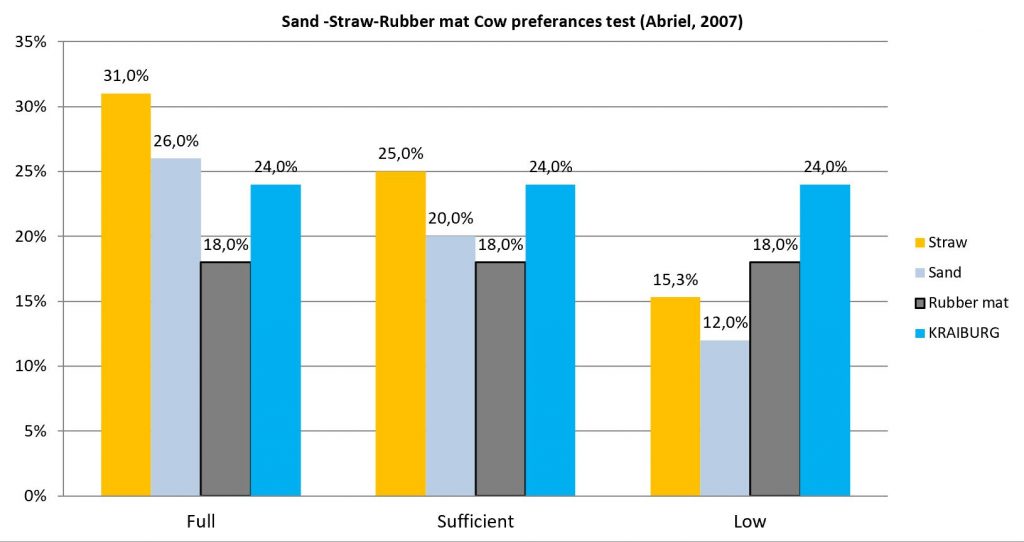
Straw cow bedding littering
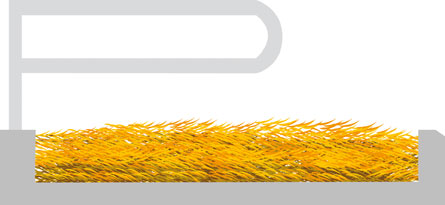
Cost comparisons of deep straw beddings / elevated rubber mattress and KRAIBURG
Cost of Deep stall with straw littering
Straw | 260kg/ cow | 30-€ /ton | 7,80-€ |
Lime | 260kg/ cow | 35-€ /ton | 9,10-€ |
Loading & removing | 10 min/ cow | 12-€/ h | 2,00-€ |
Distribution | 20 min/ cow | 12-€/ h | 4,00-€ |
Maintenance & Leveling | 245 min/cow | 12-€/ h | 49,00-€ |
Cost of ELEVATED stall with rubber mat
RUBBER Mats | *8 years life | 170 Euro/stall | 21,25 € |
Fine chopped straw | 40 kg/a | 0,18-Euro/kg | 7,20 € |
Saw dust (alternative) | 0,53 M3/a | 8-Euro/M3 | 4,25 € |
Straw | 10 min/ cow | 12-Euro/h | 2,00 € |
Maintenance | 60-90 min/cow | 12-Euro/h | 18,00 € |
ANNUAL COST | 48,45 € |
Sources: Heidenreich Thomas, oral presentation at LFL saxonia, Köllitsch,Germany 2007